Material Options
Instant Online Quote for Steel Parts
Enter your dimensions, material, finish, and features your part needs and let our Instant Quote algorithm give you immediate pricing.
Steel, Stainless Steels, Tool Steels & Alloys
Steel is an alloy that contains an iron base which is combined with carbon and other elements. In theory, all steels are iron alloys but for classification purposes there are four groups that common steels fall into: Carbon Steels, Alloy Steels, Stainless Steels and Tool Steels.
Different grades of steel can be used in many industries. Common uses include bolts, brackets, structural, enclosures, bolts, tools and many more.
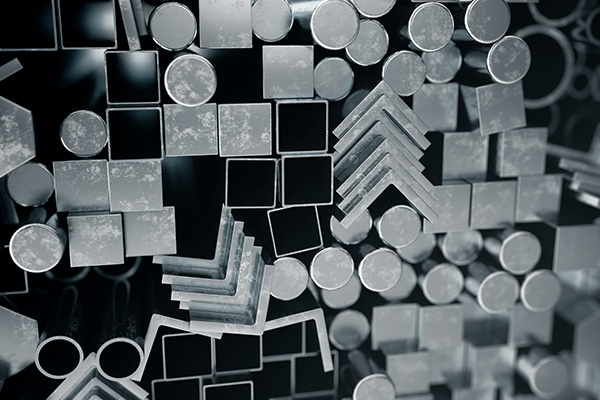
Steel, Stainless Steels, Tool Steels & Alloys grades available for CNC Machining at PartsBadger:
Mild/Low Carbon Steel
- 1008 G10080
- 1010 G10100
- 1011 G10110
- 1015 G10150
- 1018 G10180
- 1020 G10200
- 1117 G11170, 11L17 G11L17
- 1118 G11180
- 1137 G11370
- 1214 G12140, 12L14 G12144
- 1215 G12150
- A36 K02600
Medium Carbon Steel
- 1040 G10400
- 1045 G10450
- 1049 G10490
- 1050 G10500
- 1060 G10600
- 1141 G11410
- 1144 G11440
High Carbon Steel
- 1070 G10700
- 1074 G10740
- 1075 G10750
- 1080 G10800
- 1084 G10840
- 1085 G10850
- 1086 G10860
- 1090 G10900
- 1095 G10950
- 1522 G15220
- 1524 G15240
- 1526 G15260
- 1541 G15410
- 1566 G15660
& more available upon request
300 Series – Austenitic Stainless Steels
- 301 S30100, 301LN
- 302 S30200
- 303 S30300
- 304 S30400, 304L S30403, 304LN S30453, 304H S30409
- 305 S30500
- 310 S31000, 310S S31008
- 316 S31600, 316L S31603, 316LN S31653, 316Ti S31635
- 317L S31703
- 321 S32100, 321H S32109
400 Series – Martensitic Stainless Steels
- 403 S40300
- 405 S40500
- 409 S40900
- 410 S41000, 410S S41008
- 416 S41600
- 420 S42000
- 422 S42200
- 430 S43000
- 440A S44002 , 440B S44003, 440C S44004, 440F S44020
- 431 S43100
Duplex Stainless Steels
- 2001 S32001, RDN903
- 2003 S32003
- 2101 S32101, LDX2101
- 2202 S32202, DX2202
- 2205 S32205, S31803
- 2304 S32304, Duplex 2304
- 2404 S82441
- 2550 S25550, Duplex 2550
- 2507 S32750, Duplex 2507
- 2707 S32707
- 2760 S32760, Z100, Zeron 100
Precipitation Hardening Stainless Steels
- 14-4, 14-4PH
- 15-5, 15-5PH
- 17-4, 17-4PH
- 17-7, 17-7PH
Specialty Stainless Steels
- NIT50 S20910, XM-19, Nitronic 50
- NIT60 S21800, Nitronic 60
- 904L N08904
- & more available upon request
Alloy Steel
- 4027 G40270
- 4028 G40280
- 4037 G40370
- 4041 G41400
- 4042 G40420
- 4043 G40430
- 4118 G41180
- 4130 G41300
- 4135 G41350
- 4137 G41370
- 4140 G41400
- 4142 G41420
- 4145 G41450
- 4320 G43200
- 4330 G43300
- 4340 G43400
- 6150 G61500
- 8620 G86200
- 8630 G86300
- 8640 G86400
- 8650 G86500
- & more available upon request
Air Hardening – Cold Working Tool Steel
- A2, T30102, SKD12
- A3, T30103
- A4, T30104
- A6, T30106
- A7, T30107
- A8, T30108
- A9, T30109
- A10, T30110
High Carbon, High Chromium, Tool Steel
- D2, T30402, SKD11
- D3, T30403, SKD1
- D4, T30404
- D5, T30405
- D7, T30407
Oil Hardening Tool Steel
- O1, T31501, SKD1
- O2, T31502, BO2
- O6, T31506
- O7, T31507
Chromium Hot-Work Steel
- H10, T20810
- H11, T20811
- H12, T20812
- H13, T20813
- H14, T20814
- H19, T20819
Tungsten Hot-Work Tool Steel
- H21, T20821
- H22, T20822
- H23, T20823
- H24, T20824
- H25, T20825
- H26, T20826
Molybdenum Hot-Work Tool Steel
- H42, T20842
Shock-Resisting Tool Steel (Shockproof)
- S1, T41901
- S2, T41902
- S5, T41905
- S6, T41906
- S7, T41907
Low Alloy Specialty Tool Steel
- L2, T61202, 115CrV3, 1.2210
- L6, T61206, SKT4, 1.2713
Low Carbon Mold Steel
- P2, T51602
- P3, T51603
- P4, T51604
- P6, T51606
- P20, T51620
- P21, T51621
Water Hardening Tool Steel
- W1, T72301
- W2, T72302
- W3, T72305
Steel, Stainless Steels, Tool Steels & Alloys surface finishes for CNC machined parts:
Deburr/Mill
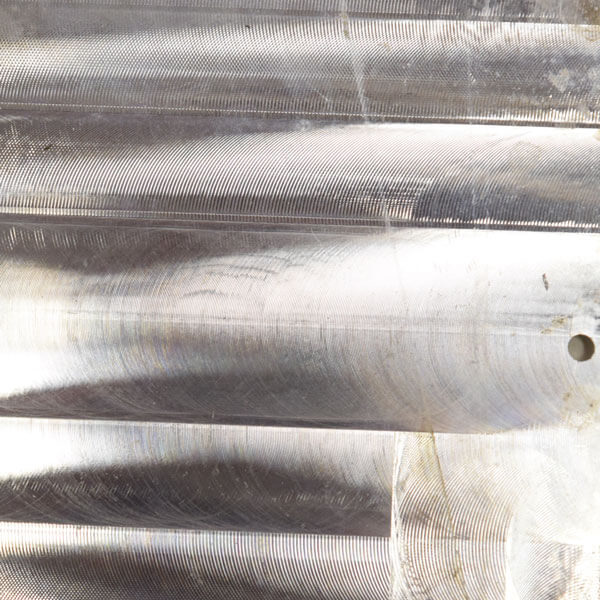
Rough Polish
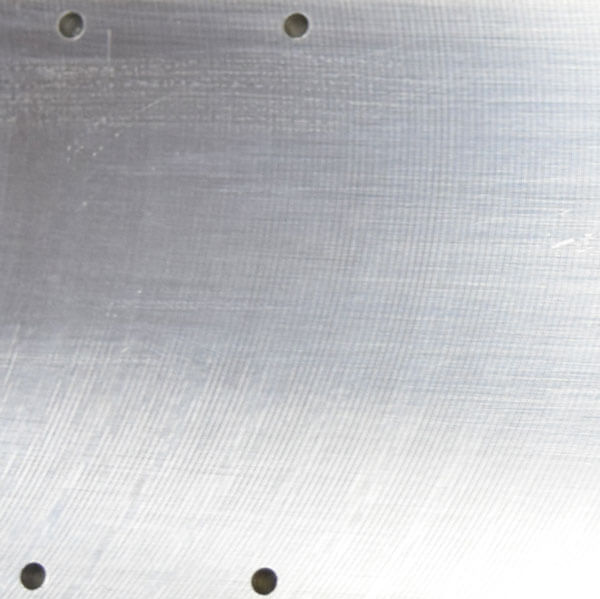
Bead Blast
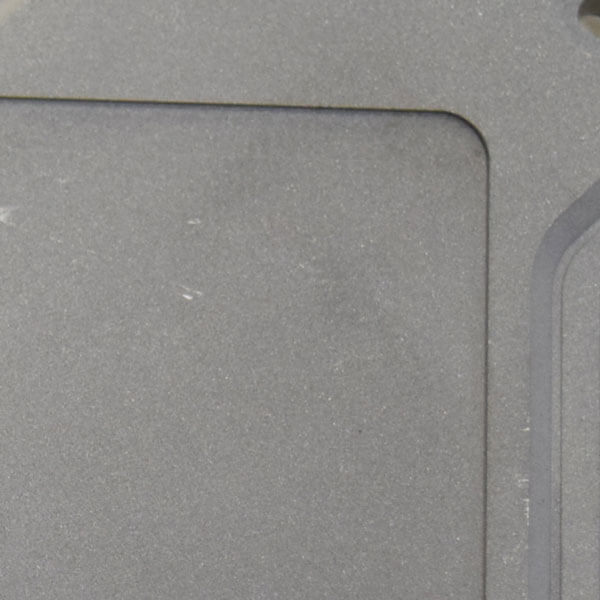
Knurling
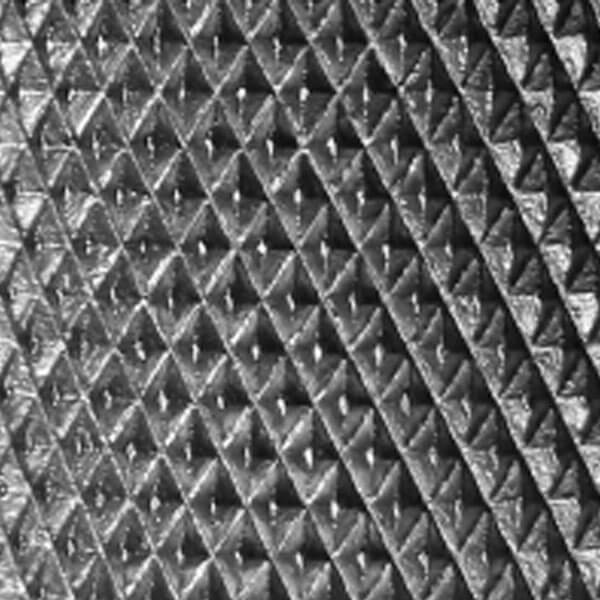
Brushing
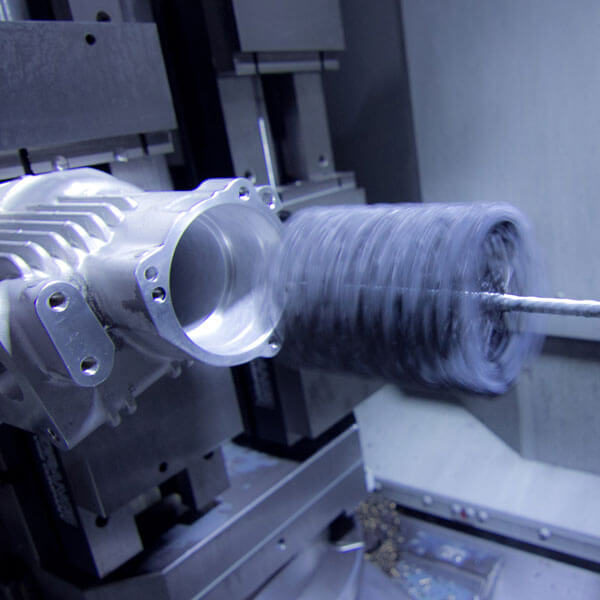
Tumbling
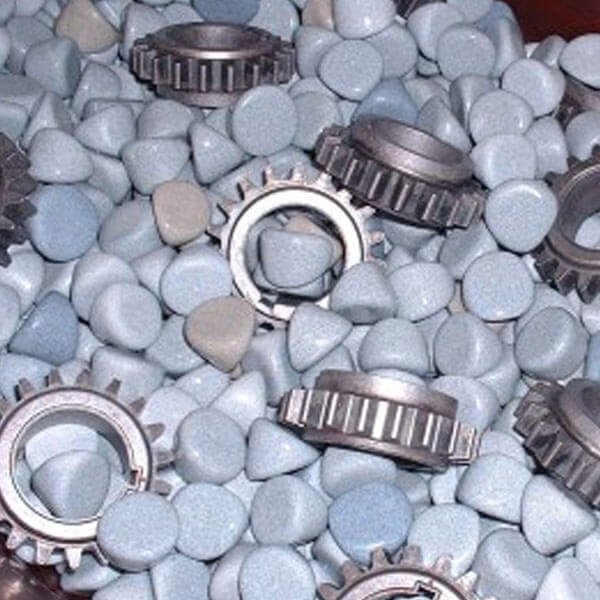
Surface treatments available for CNC machined parts:
Anodizing
Sulfuric Anodize MIL-A-8625/Type II
Type II, Class 1 ; Type II, Class 2
Hard Anodize MIL-A-8625/Type III
Type III, Class 1 ; Type III, Class 2
Anodizing creates a thin oxidized layer that may be dyed a certain color. Anodizing is only available on Aluminum or Stainless Steel materials. Anodizing will make the surface non-conductive. Type I thin or Type III thick anodizing is available. Colors include: Clear, Black, Red, Blue, Orange, Purple, Green, and Brown.
Chromate Conversion/Alodine
MIL-DTL-5541 ; Hexavalent Yellow and Trivalent Clear
Type I, Class 1A ; Type I, Class 3
Type II, Class 1A ; Type II, Class 3
Chromate Coating provides additional corrosion resistance or as a primer for powder coating while maintaining conductivity. Chromate coatings are soft and gelatinous when first applied, but harden and become hydrophobic as they age. This process creates an iridescent or yellow tint to the part.
Electropolishing
ASTM-B-912
One of the benefits of electropolishing for stainless stee, is that it removes iron from the surface and enhances the chromium/nickel content. This process creates a mirror like finish on the part, creating a higher polish than what can be created manually. Surface quality obtained by Electropolishing is directly related to the quality of the pre-electropolished surface. Electropolishing cannot remove digs, gouges, scratches or other similar surface distortions.
Passivation
ASTM A967, AMS2700, ASTM A380
Passivation uses a nitric or citric acid to create a protective oxide layer on parts made from austenitic, ferritic, and martensitic corrosion-resistant steels. The protective layer helps improve the corrosion resistant qualities of the metals.
Nickel and Silver Electroplating
Electroplating adds a thin layer of metal onto another metal object. The plated layer can be decorative, provide corrosion resistance, wear resistance, or used to build up worn or undersized parts for salvage purposes.
Ceramic Coating
We offer various brands of ceramic coating. Cerakote (H-240) is a Polymer-Ceramic Composite ceramic coating that can be applied to metals, plastics, polymers and wood. The unique formulation used for Cerakote ceramic coating enhances a number of physical performance properties including abrasion/wear resistance, corrosion resistance, chemical resistance, impact strength, and hardness.
Learn more about the properties of Steel and its Alloys:
Steels: Defining the types, grades and classifieing series.
Steel is an alloy that contains an iron base which is combined with carbon and other elements. In theory, all steels are iron alloys but for classification purposes there are four groups that common steels fall into: Carbon Steels, Alloy Steels, Stainless Steels and Tool Steels.
Carbon Steels
Carbon steels are primarily alloyed with carbon and account for roughly 90% of all steel production in the world. To be classified as a carbon steel, it must abide by the following:
- Contains no noted chromium, cobalt, molybdenum, nickel, niobium, titanium, tungsten, vanadium or zirconium.
- Contains no more than 0.60% copper
- Contains no more than 1.65% manganese
- Contains no more than 0.60% silicon
Earth is made up of roughly 35% Iron by mass. The majority of which is in Earths solid core.
Depending on the content of carbon in the steel, it can fall into one of three groups:
- Low Carbon Steels/Mild Steels contain up to 0.3% carbon
- Medium Carbon Steels contain 0.3-0.6% carbon
- High Carbon Steels contain more than 0.6% carbon
No carbon steel can contain more than 2.1% carbon by weight. Sometimes carbon steels can be categorized as alloy steels, but technically they should fall into two separate groups.
Carbon & Alloy Steel SAE Series:
1000 Series– Carbon steels
2000 Series– Nickel steels
3000 Series– Nickel-chromium steels
4000 Series– Molybdenum steels
5000 Series– Chromium steels
6000 Series– Chromium-vanadium steels
7000 Series– Tungsten steels
8000 Series– Nickel-chromium-molybdenum steels
9000 Series– Silicon-manganese steels
Stainless Steels
Stainless Steels (sometimes known as inox steels) are known for their corrosion resistance and contain a minimum of 10.5% chromium and a maximum of 1.2% carbon by mass. The higher the chromium content, the higher the corrosion resistance. Many other elements can be added to increase or decrease certain properties, but all stainless steel grads fall into one of four main categories.
- Contain high levels of chromium and nickel
- Typically non-magnetic (can become slightly magnetic after cold working)
- Excellent corrosion resistance
- High ductility / formability
- Weldable
- Cannot be heat treated, but cold working can add significant strength
- Classified in the 200 & 300 series of stainless steels
- Contain high levels of chromium (no nickel)
- Strongly magnetic
- Good corrosion resistance (can be improved by increasing chromium and molybdenum)
- Good ductility, toughness and weldability (can be improved by decreasing carbon and nitrogen)
- Cannot be heat treated, but cold working can add significant strength
- Classified in the 400 series of stainless steels
- Due to containing less chromium and nickel than austenitic steels, ferritic steels are typically less expensive
- Contain high levels of chromium and smaller levels of carbon
- Typically are strongly magnetic (certain hardened martensitic steels lose their magnetism)
- Fair corrosion resistance, not as good as ferritic or austenitic steels
- Can be hardened to extreme strengths, although this can reduce toughness and makes it brittle
- In some grades, the carbon is replaced with nickel to increase toughness and corrosion resistance
- Commonly used in engineering and wear-resistant applications. Pocket knives are made out of martensitic steels
- Classified in the 400 series of stainless steels
- Contain roughly a 50/50 mix of austenite and ferrite
- Typically magnetic
- Excellent corrosion resistance
- Excellent strength and fabrication properties
- Machining can be more difficult due to strength, but is still possible
Stainless Steel SAE Series:
Type 102– Austenitic general purpose stainless steel
200 Series– Austenitic chromium-nickel-manganese alloys
300 Series– Austenitic chromium-nickel alloys
400 Series– Ferritic and martensitic chromium alloys
500 Series– Heat-resisting chromium alloys
Alloy Steels:
Technically, stainless steels and tool steels can be considered alloy steels. But for the sake of grouping them separately, alloy steels are steels that meet one of the following conditions:
- Contains more than 1.65% maganese, 0.60% silicon, or 0.60% copper
- Contains any specified amount of any other element to obtain an alloying effect. If the alloy steel contains chromium, it must be less than 3.99%
In general, alloying elements are added in lower percentages (less than 5%) to increase strength. When elements make up over 5% of the alloy it is usually to obtain special properties such as corrosion resistance, temperature stability or machinability.
How certain elements affect alloy steels:
Bismuth– Improves machinability
Boron– Significantly improves hardenability
Chromium– Increases hardenability and corrosion resistance
Copper– Improves corrosion resistance
Lead– Improves machinability
Manganese– Reduces brittleness and increases hardenability
Nickel– Increases corrosion resistance and toughens
Silicon– Increases strength and improves magnetic properties
Tungsten– Increases melting point
Tool Steel
Tool steel refers to certain carbon and alloy steels that have significant hardness and resistance to high temperatures, abrasion and deformation. They are commonly used in the shaping of other materials.
Depending on what properties are required, there are six groups of tool steels. Water hardening, air hardening, high carbon chromium, shock resisting, oil hardening and hot working. Hot working steels (H series) are the only ones designed for use at high temperatures and all other groups are typically used at room temperature but can be appropriate for applications up to 300°F.
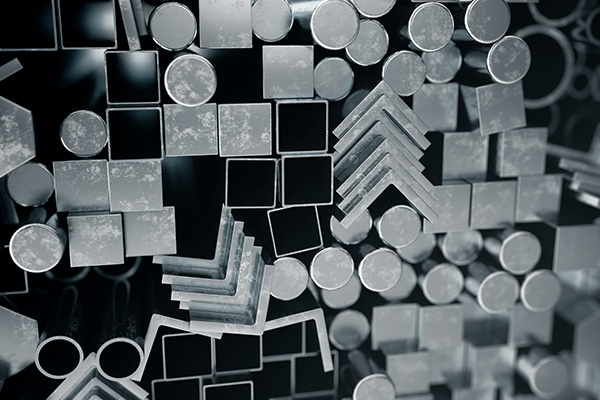
Water Hardening (W Series)
Water hardening steels are hardened by water quenching and are the most common tool steel due to their low cost. They can maintain significant hardness but tend to be more brittle when compared to other tool steels. Around 300°F these steels begin to soften and are generally not suited for high temperature applications.
Air Hardening (A Series)
Air hardening steels are known to be all purpose tool steels that contain a high amount of chromium to reduce distortion during the heat treatment process. They have great machinability, wear resistance and toughness and are known to be a good balance between D series and A series tool steels.
High Carbon-Chromium (D Series)
Containing high amounts of carbon and chromium (10-13%), the D series tool steels retain their hardness up to roughly 800°F and are commonly used in forges and die-casting applications. Having a high chromium content they can sometimes be classified as stainless, however D series tool steels have a very limited corrosion resistance.
Shock Resisting (S Series)
Shock resisting steels can resist high volumes of shock at both high and low temperatures, where other tool steels may tend to crack in these conditions. They contain a low amount of carbon (0.5%) and varying amounts of molybdenum, tungsten, chromium, silicon and manganese. A common use of S series steels is in jackhammer bits.
Hot Working (H Series)
Hot working steels are designed to cut or shape other materials at high temperatures. They maintain high levels of strength and hardness during long exposure to elevated temperatures. They contain a low amount of carbon and a moderate amount of other alloying elements.
Oil Hardening (O Series)
O Series steels are hardened in oil at around 1450°F and then tempered at cooler temperatures (less than 400°F). They are typically used in woodworking tools, cutting tools and knives and can be hardened up to 66 HRC.