Material Options
Instant Online Quote for Aluminum Parts
Enter your dimensions, material, finish, and features your part needs and let our Instant Quote algorithm give you immediate pricing.
Aluminum
When considering which alloy to use for machining processes we need to understand how the added elements affect the alloys machinability. Machinability is a loose term but general stands for the ease of which the alloy can be machined.
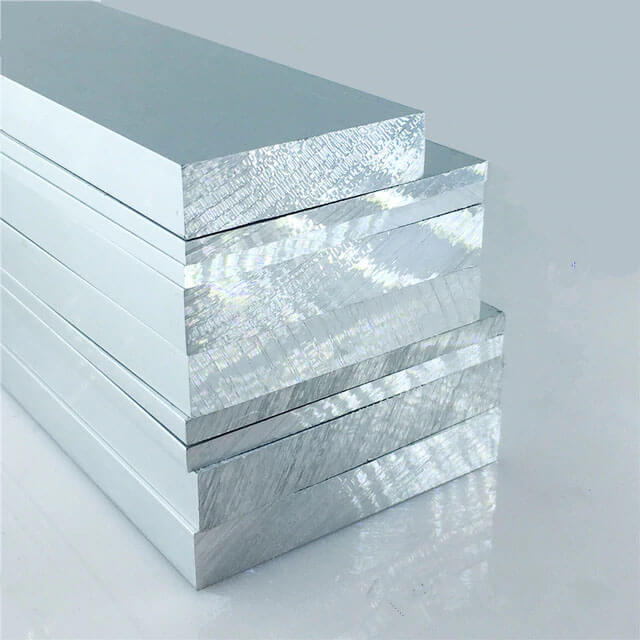
Aluminum grades available for CNC Machining at PartsBadger:
2000 Series Aluminum
- 2011, 2011-0
- 2011-T3
- 2011-T6
- 2011-T8
- 2024, 2014-0
- 2024-T3
- 2024-T351
- 2024-T6
- 2024-T851
3000 Series Aluminum
- 3003, 3003-0
- 3003-H12
- 3003-H14
- 3003-H16
- 3003-H18
- 3003-H32
5000 Series Aluminum
- 5052, 5052-0
- 5052-H32
- 5052-H34
- 5052-H38
6000 Series Aluminum
- 6061, 6061-0
- 6061-T4
- 6061-T6
- 6061-T6511
- 6061-T8
- 6063, 6063-0
- 6063-T4
- 6063-T5
- 6063-T52
- 6063-T6
7000 Series Aluminum
- 7050, 7050-0
- 7050-T3511
- 7050-T7451
- 7050-T452
- 7050-T651
- 7075, 7075-0
- 7075-6
- 7075-73
Cast & Jig Plate
- MIC-6
- ATP 5
- & more available upon request
Aluminum surface finishes for CNC machined parts:
Deburr/Mill
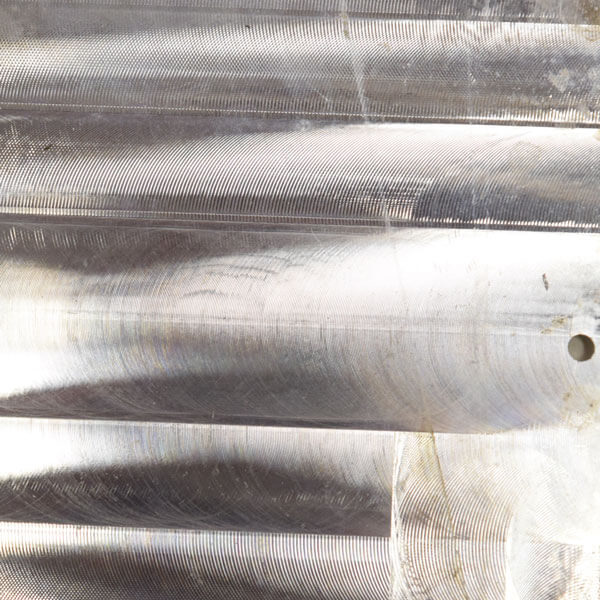
Rough Polish
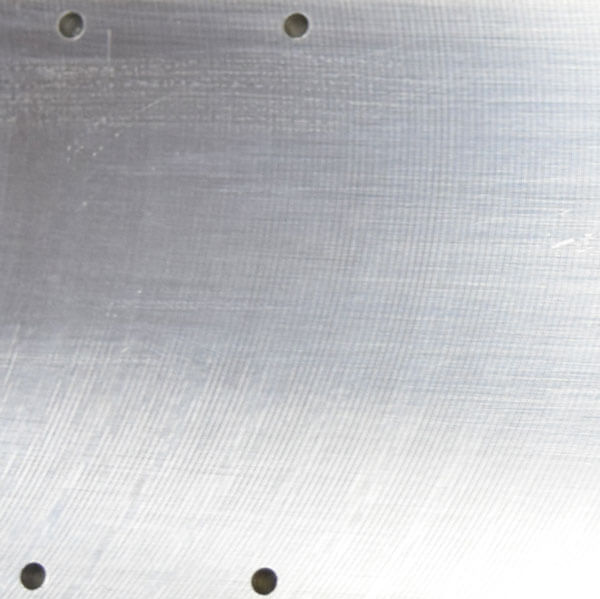
Bead Blast
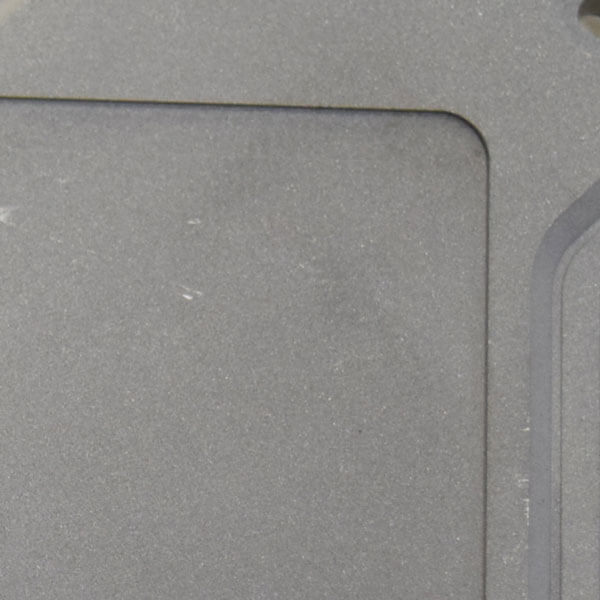
Knurling
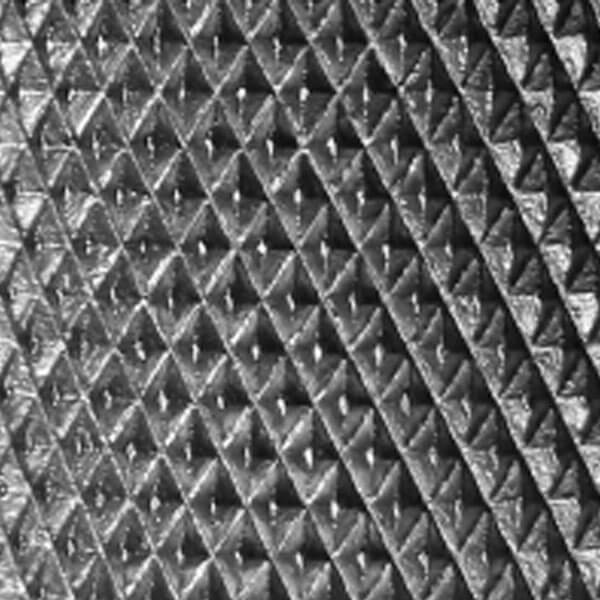
Brushing
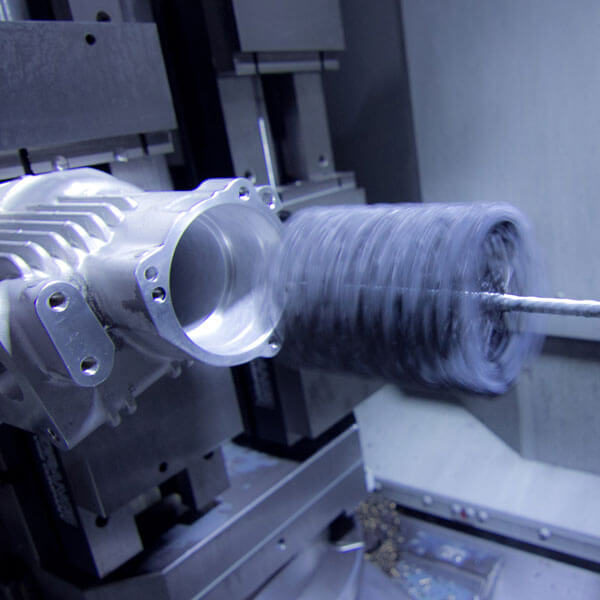
Tumbling
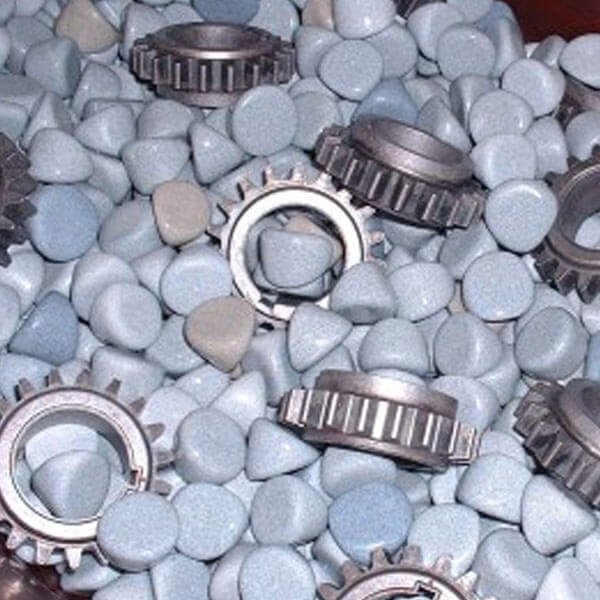
Available Surface Treatements for CNC machined parts:
Anodizing
Sulfuric Anodize MIL-A-8625/Type II Type II, Class 1 ; Type II, Class 2 Hard Anodize MIL-A-8625/Type III Type III, Class 1 ; Type III, Class 2 Anodizing creates a thin oxidized layer that may be dyed a certain color. Anodizing is only available on Aluminum or Stainless Steel materials. Anodizing will make the surface non-conductive. Type I thin or Type III thick anodizing is available. Colors include: Clear, Black, Red, Blue, Orange, Purple, Green, and Brown.
Chromate Conversion/Alodine
MIL-DTL-5541 ; Hexavalent Yellow and Trivalent Clear Type I, Class 1A ; Type I, Class 3 Type II, Class 1A ; Type II, Class 3 Chromate Coating provides additional corrosion resistance or as a primer for powder coating while maintaining conductivity. Chromate coatings are soft and gelatinous when first applied, but harden and become hydrophobic as they age. This process creates an iridescent or yellow tint to the part.
Electropolishing
ASTM-B-912 One of the benefits of electropolishing for stainless stee, is that it removes iron from the surface and enhances the chromium/nickel content. This process creates a mirror like finish on the part, creating a higher polish than what can be created manually. Surface quality obtained by Electropolishing is directly related to the quality of the pre-electropolished surface. Electropolishing cannot remove digs, gouges, scratches or other similar surface distortions.
Passivation
ASTM A967, AMS2700, ASTM A380 Passivation uses a nitric or citric acid to create a protective oxide layer on parts made from austenitic, ferritic, and martensitic corrosion-resistant steels. The protective layer helps improve the corrosion resistant qualities of the metals.
Nickel and Silver Electroplating
Electroplating adds a thin layer of metal onto another metal object. The plated layer can be decorative, provide corrosion resistance, wear resistance, or used to build up worn or undersized parts for salvage purposes.
Ceramic Coating
We offer various brands of ceramic coating. Cerakote (H-240) is a Polymer-Ceramic Composite ceramic coating that can be applied to metals, plastics, polymers and wood. The unique formulation used for Cerakote ceramic coating enhances a number of physical performance properties including abrasion/wear resistance, corrosion resistance, chemical resistance, impact strength, and hardness.
Learn more about the properties of Aluminum and its Alloys
Aluminum
Aluminum (AI) is a soft silvery-white and nonmagnetic element that is known to be the top metal choice for many industrial uses. Its properties include high strength, low density and can be resistance to corrosion through a process called Passivation.
Aluminum Alloys
In order to enhance or add certain properties, Aluminum is commonly combined with other elements to form Aluminum alloys. Within these alloys, Aluminum is the predominant Material. To be considered an Aluminum alloy, the additional elements added must not exceed a total of 15% of the overall composition. Depending on which elements are added to the aluminum, the resulting alloy can have many different strengths and weaknesses. When considering which alloy to use for machining processes we need to understand how the added elements affect the alloys machinability. Machinability is a loose term but general stands for the ease of which the alloy can be machined.
Earth is made up of 1.59% Aluminum by mass. The majority of which is in the Earth’s crust.
How certain elements affect the machinability of aluminum alloys:
Defining the different series of Aluminum Alloys:
2000 Series– Alloyed primarily with Copper and can be hardened to strengths similar to steel. Often used in aerospace applications.
3000 Series– Alloyed primarily with Manganese and can be hardened and heat treated. Often used in beverage cans, cookware and industrial high heat applications.
4000 Series- Alloyed primarily with Silicon. Often used in applications where a lower melting point in the alloy is needed, such as casting and welding. If Magnesium is added to a 4000 series alloy it can be heat treated and transformed into a 6000 series alloy.
5000 Series– Alloyed primarily with Magnesium and offers high corrosion resistance. Often used in marine applications. 5083 alloy is common and has the highest strength of non heat treated alloys.
6000 Series- Alloyed primarily with a combination of Magnesium and Silicon and can be one of the most versatile of the Aluminum Alloys. It is considered an all-purpose aluminum due to its high machinability and strength. 6061 alloy is the most common of all Aluminum alloys and is used in many applications.
7000 Series– Alloyed primarily with Zinc and can be hardened to the highest strength of any Aluminum alloy. Often used in aerospace applications.
Common Industry Uses
Aerospace / Aircraft
With properties including high strength, light weight and efficient heat transfer, the following alloys are common in aerospace and aircraft applications.
- 1420
- 2004, 2014, 2017, 2020, 2024, 2080, 2090, 2091, 2095, 2219, 2324, 2519, 2524
- 4047
- 6013, 6061, 6063, 6113, 6951
- 7010, 7049, 7050, 7055, 7068, 7075, 7079, 7093, 7150, 7178, 7475
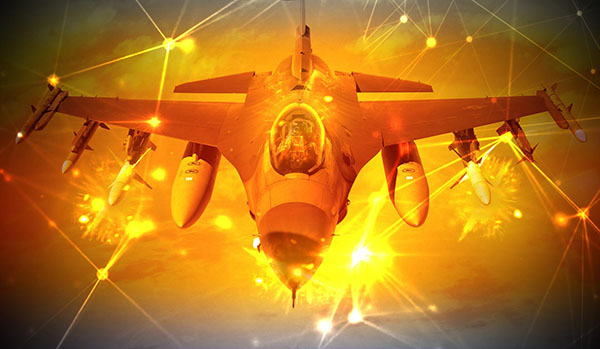
Marine / Offshore
Non heat treated alloys (5000 series) are preferred in marine applications due to their high corrosion resistance. Magnesium adds both strength and corrosion resistance as well as increasing the ability to be welded. In high humidity, underwater and salt water environments, the following alloys are popular:
- 5052, 5059, 5083, 5086
- 6061, 6063
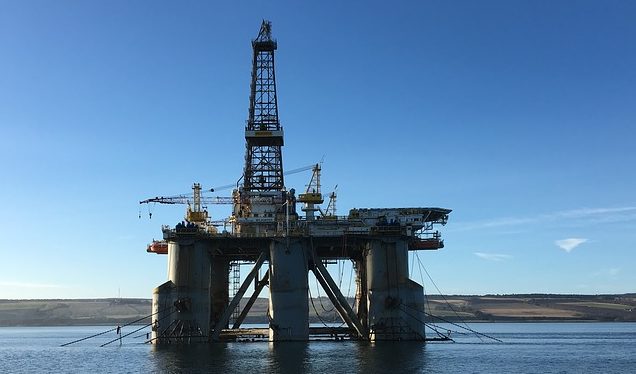
Automotive / Cycling
Due to their light weight and strength, the following allows are preferred for cycling frames and parts.
- 2014
- 6061, 6063
- 7005, 7075
For automotive manufacturing, aluminum alloys are the first choice for external body parts and other components.
- 2008, 2036, 5083, 5456, 5754, 6016, 6111 are common alloys for body panels.
- 5182, 5754, 6061, 6063 are common alloys for automobile frames
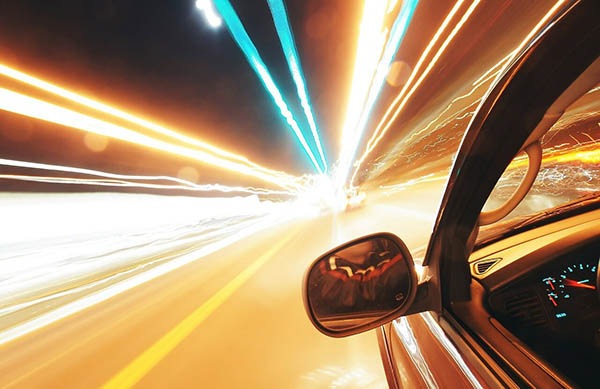