Material Options
Instant Online Quote for Brass Parts
Enter your dimensions, material, finish, and features your part needs and let our Instant Quote algorithm give you immediate pricing.
Brass
Brass is an alloy comprised of copper and zinc and offers a wide range of properties such as high corrosion resistance, hardness, thermal conductivity, strength, and workability. It is considered low friction and non-magnetic alloy and can range in colors from deep red to golden yellow.
Different grades of brass can be used in many industries. Common uses include nuts, bolts, threaded parts, electrical terminals, taps, and injector parts.

Copper, Brass and Bronze grades available for CNC Machining at PartsBadger:
100 Series
- C10000-C15999 – Coppers
- C100, CW003A
- C101, CW004A, CW011A, CW012A, CW013A, HDHC Copper
- C102, CW005A, Farmers Copper
- C103, CW008A, CW017A. CW019A, Oxygen Free Copper
- C104, CW006A
- C105, Oxygen Free with Silver
- C106, CW024A, DHP, Engineering Copper
- C109, CW118C, Tellurium Copper
- C110, CW109C, CW111C, CW112C, Silicon Copper
- C111, C11100, CW114C, Sulphur Copper
- C113, C11300, CW108C
- C114, C11400
- C122, C12200, DHP Copper
- C145, C14500, Telluirum Copper
- C147, C14700, Sulfur Bearing Copper
- C16000-C19999 – High Copper Alloys
- C172, C17200, CW100C, CW101C, CW102C, C173, C175, C180, C181, CuBe2, Beryllium Copper
- C182, C18200, CW105C, CW106C, CCZ, Copper Chrome, Zirconium
- C187, C18700, Leaded Copper
- C191, C19160, Leaded Nickel Copper
200 Series – C20000 – Brasses
- C210, C21000, Gliding Brass
- C220, C22000, Commercial Brass
- C230, C23000, Red Brass
- C260, C26000, Olin Brass, Cartridge Brass
- C272, C27200, Yellow Brass
- C274, C27450, Yellow Brass
300 Series – C30000, Leaded Brasses
- C314, C31400, Leaded Commercial Bronze
- C330, C33000, Low Leaded Brass
- C335, C33500, Low Leaded Brass
- C353, C35300, High Leaded Brass
- C360, C36000, Free Machining Brass, Free Cutting Brass
- C365, C36500, Leaded Muntz
- C385, C38500, Architectural Bronze
400 Series – C40000 – Tin Brasses
- C443, C44300, Admiralty Brass
- C464, C46400, Naval Brass
- C485, C48500, Leaded Naval Brass
500 Series – C50000, Phosphor Bronzes
- C510, C51000, Phosphor Bronze
- C544, C54400, Phosphor Bronze
600 Series – C60000, Bronzes
- C623, C62300, Aluminum Bronze
- C624, C62400, Aluminum Bronze
- C625, C62500, Aluminum Bronze
- C630, C63000, Aluminum Nickel Bronze
- C642, C64200, Aluminum Silicon Bronze
- C651, C65100, Silicon Bronze
- C655, C655000, Silicon Bronze
- C655, C65500, High Silicon Bronze
- C673, C67300, Manganese Bronze
- C675, C67500, Manganese Bronze
- C676, C67600, Manganese Bronze
- C693, C69300, Eco Brass
700 Series – C70000, Copper Nickels, Nickel Silvers
- C725, C72500, Copper Nickel
- C752, C75200, Nickel Silver
- C770, C77000, Nickel Silver
- C792, C79200, Leaded Nickel Silver
- C798, C79800, Leaded Nickel Silver
800 Series
- C80000-C81399 Coppers
- C81400-C83299 High Copper Alloys
- C83300-C89999 Brasses
- C863, C86300, Manganese Bronze
900 Series
- C90000-C95999, Bronzes
- C932, C93200, Bearing Bronze
- C954, C95400, Aluminum Bronze
- C96000-C96999, Copper Nickels
- C97000-C97999, Nickel Silvers
- C98000-C98999, Leaded Coppers
- C99000-C99999, Special Alloys
- C993, C993000, Incramet 800
- C997, C99700, White Manganese Brass
Copper, Brass and Bronze surface finishes for CNC machined parts:
Deburr/Mill
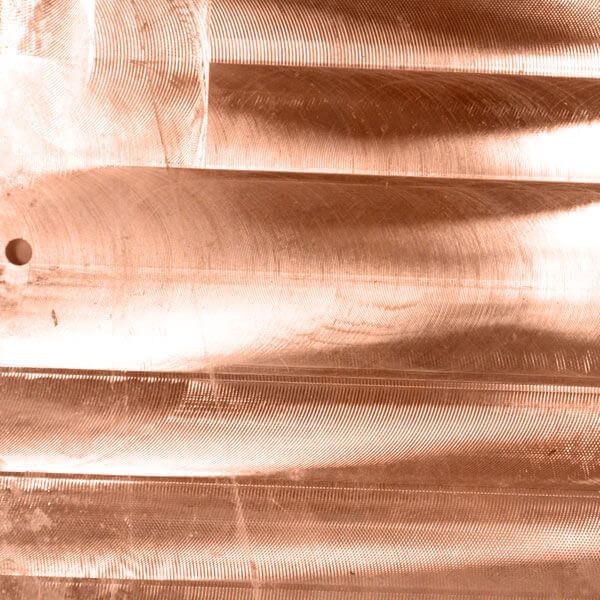
Rough Polish
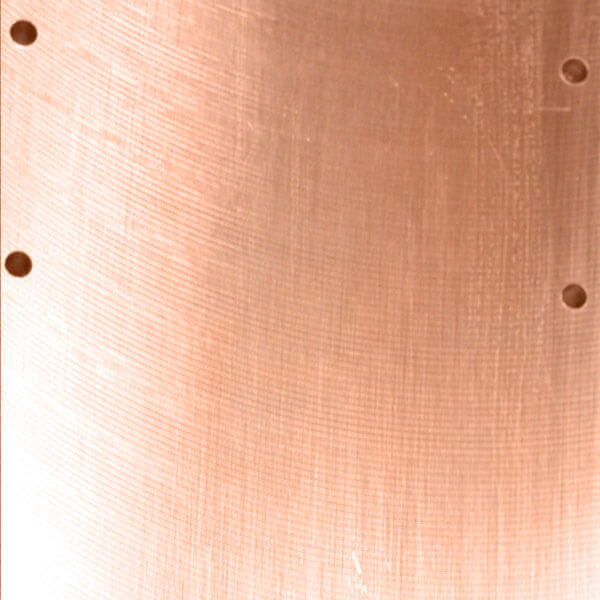
Bead Blast
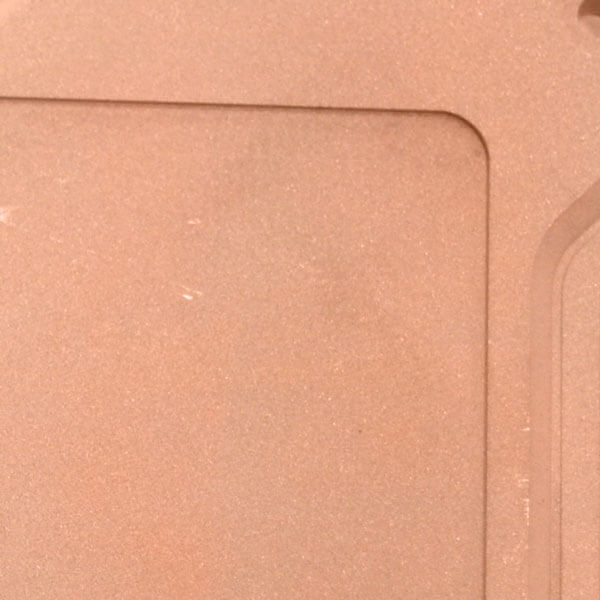
Knurling
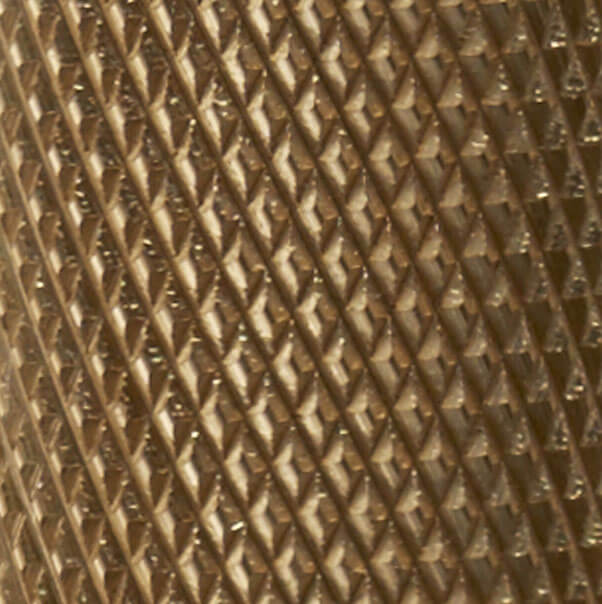
Brushing
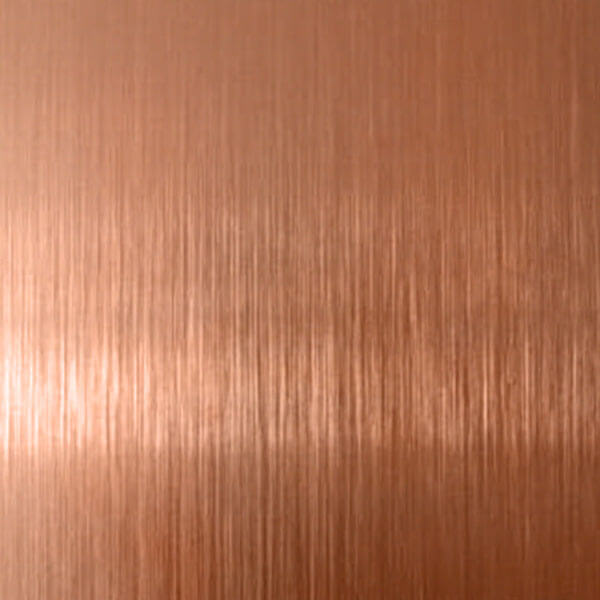
Tumbling
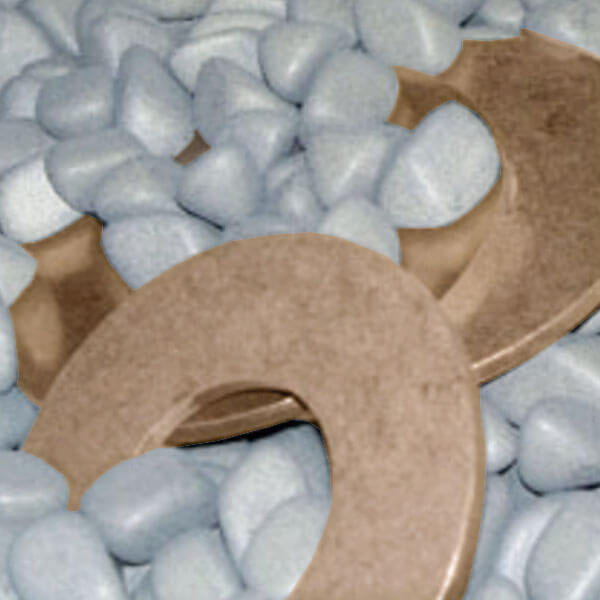
Surface treatments available for CNC machined parts:
Anodizing
Sulfuric Anodize MIL-A-8625/Type II
Type II, Class 1 ; Type II, Class 2
Hard Anodize MIL-A-8625/Type III
Type III, Class 1 ; Type III, Class 2
Anodizing creates a thin oxidized layer that may be dyed a certain color. Anodizing is only available on Aluminum or Stainless Steel materials. Anodizing will make the surface non-conductive. Type I thin or Type III thick anodizing is available. Colors include: Clear, Black, Red, Blue, Orange, Purple, Green, and Brown.
Chromate Conversion/Alodine
MIL-DTL-5541 ; Hexavalent Yellow and Trivalent Clear
Type I, Class 1A ; Type I, Class 3
Type II, Class 1A ; Type II, Class 3
Chromate Coating provides additional corrosion resistance or as a primer for powder coating while maintaining conductivity. Chromate coatings are soft and gelatinous when first applied, but harden and become hydrophobic as they age. This process creates an iridescent or yellow tint to the part.
Electropolishing
ASTM-B-912
One of the benefits of electropolishing for stainless stee, is that it removes iron from the surface and enhances the chromium/nickel content. This process creates a mirror like finish on the part, creating a higher polish than what can be created manually. Surface quality obtained by Electropolishing is directly related to the quality of the pre-electropolished surface. Electropolishing cannot remove digs, gouges, scratches or other similar surface distortions.
Passivation
ASTM A967, AMS2700, ASTM A380
Passivation uses a nitric or citric acid to create a protective oxide layer on parts made from austenitic, ferritic, and martensitic corrosion-resistant steels. The protective layer helps improve the corrosion resistant qualities of the metals.
Nickel and Silver Electroplating
Electroplating adds a thin layer of metal onto another metal object. The plated layer can be decorative, provide corrosion resistance, wear resistance, or used to build up worn or undersized parts for salvage purposes.
Ceramic Coating
We offer various brands of ceramic coating. Cerakote (H-240) is a Polymer-Ceramic Composite ceramic coating that can be applied to metals, plastics, polymers and wood. The unique formulation used for Cerakote ceramic coating enhances a number of physical performance properties including abrasion/wear resistance, corrosion resistance, chemical resistance, impact strength, and hardness.
Learn more about the properties of Copper and its Alloys
Copper
Copper (Cu) is one of the few elements that appears in nature in a usable metallic form. It is a soft, malleable and ductile metal that has high thermal and electrical conductivity. It has a pinkish orange color and can be found naturally in many places around the world.
Copper Alloys
In order to enhance or add certain properties, copper is commonly combined with other elements to form copper alloys. Within these alloys, copper is the predominant material but the alloying elements can makeup up over 40% of the alloys composition. The most common alloying element in high amounts is zinc.
Depending on which elements are added to the copper the name of the alloy will also change. The most common copper alloys are brass, bronze, copper-nickel, leaded copper, nickel-silver and gunmetal among many others.
Copper has been in use at least 10,000 years, but more than 95% of all copper ever mined and smelted has been extracted since 1900, and more than half was extracted in the last 24 years
Common Types of Copper Alloys:
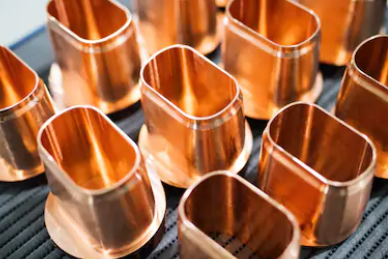
High Copper Alloys
High copper alloys consist of materials containing a copper amount between 96%-99.3%. They maintain the high electrical and thermal conductivity due to the high copper contents but also gain properties of the alloying elements. High copper alloys are used more in casting and forming applications than they are in machining.
Common high copper alloys include:
- Cadmium coppers
- Beryllium coppers
- Chromium coppers
- Zirconium copper
- Chromium-zirconium copper
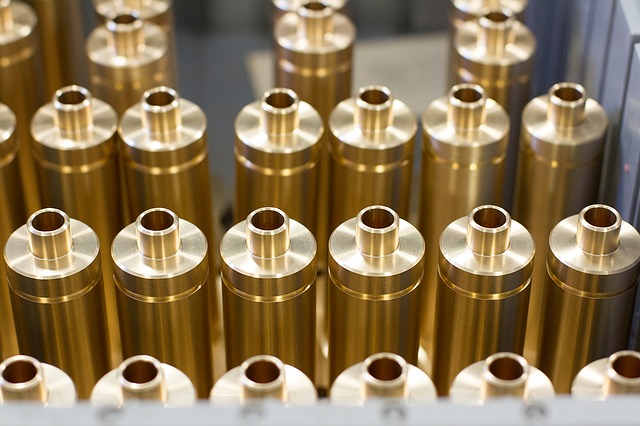
Brass
When copper is primarily alloyed with zinc it is refereed to as brass. The zinc content can vary but it is typically kept under 15% to maintain corrosion resistance in the alloy. Lead is also added in smaller quantities to increase machinability. Brass is known to be strong, machinable, conductive and corrosion resistant.
Common brasses include:
- Free cutting brass
- Gliding metal (red brass)
- Engraving Brass
- Arsenical brass
- High tensile brass
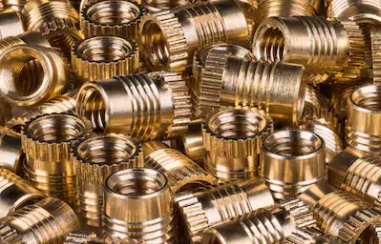
Bronze
When copper is primarily alloyed with tin, aluminum or sometimes silicon it is refereed to as bronze. Known for high strength, ductility, thermal conduction, hardness, corrosion resistance and low friction properties, bronzes are commonly used in bearings, tools, coins, sculptures and musical instruments.
Common types of bronze:
- Aluminum bronze
- Phosphor bronze
- Nickel silver
- Silicon bronze
- Copper nickel
Machining Copper, Brass and Bronze:
When referring to metals that are often used in machining, the term free machining or free cutting is often used. Free machining materials contain certain elements that add efficiencies such as higher machining speed, improved surface finish, smaller chips and longer tool life.
Lead is has been historically added to alloys to improve machinability and can act as a lubricant and assists in chip breaking. However with recent developments in the negative health implications of lead, free machining coppers, brasses and bronzes are being transitioned to contain sulfur or tellurium instead of lead.
Unified Numbering System (UNS) for Copper and Copper Alloys
Wrought Alloys
Coppers (C10100 – C15999)
High Copper Alloys (C16000 – C19999)
Brasses (C20000 – C49999)
Bronzes (C50000 – C69999)
Copper Nickels (C70000 – C73499)
Nickel Silvers (C73500 – C79999)
Cast Alloys
Coppers (C80000 – C81399)
High Copper Alloys (C81400 – C83299)
Brasses (C83300 – C89999)
Bronzes (C90000 – C95999)
Copper Nickels (C96000 – C96999)
Nickel Silvers (C97000 – C97999)
Leaded Coppers (C98000 – C98999)
Special Alloys (C99000 – C99999)