Surface Finish: What are Your Options?
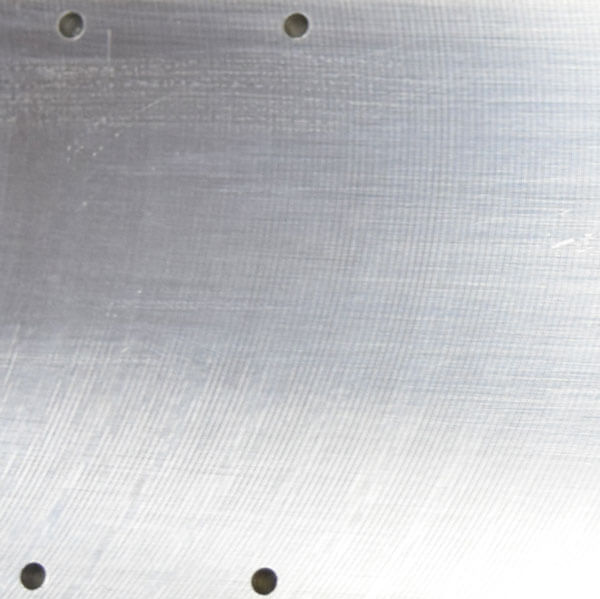
Rough Polish
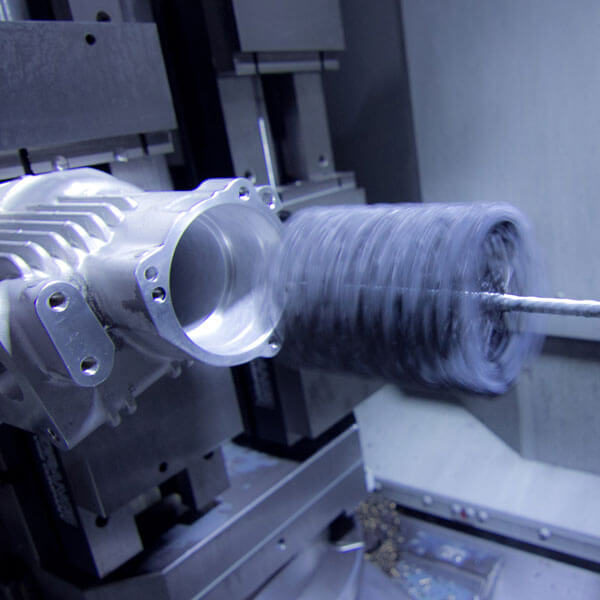
Brushing
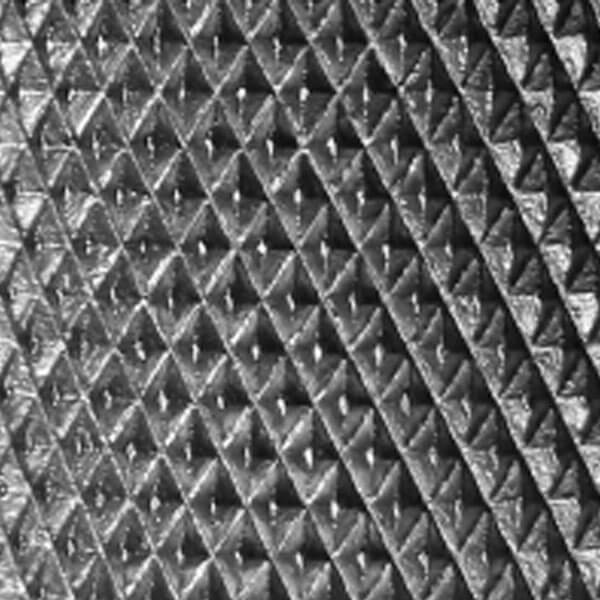
Knurling
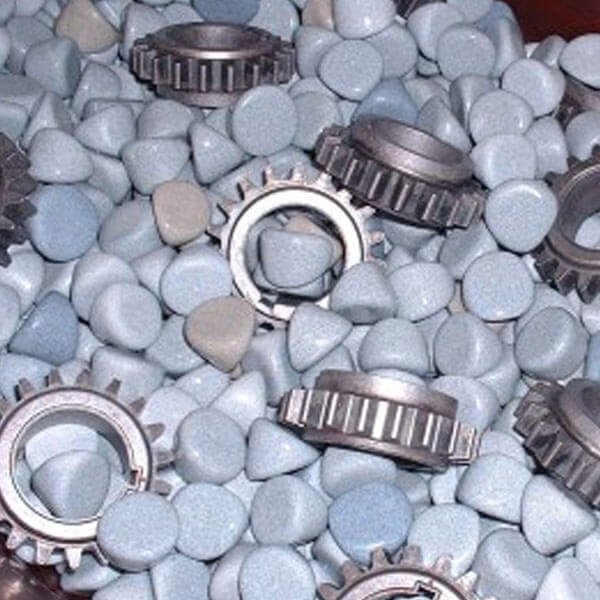
Tumbling
Surface finish, also known as surface texture, is the state of a surface by three characteristics: lay, surface roughness, and waviness.
Each manufacturing process produces a surface finish. The process is usually optimized to ensure that the resulting texture is usable. If necessary, an additional process will be added to modify the initial texture. The latter process may be grinding (abrasive cutting), polishing, lapping, abrasive blasting, honing, electrical discharge machining (EDM), milling, lithography, industrial etching/chemical milling, laser texturing, or other processes.
Lay is the direction of the predominant surface pattern, ordinarily determined by the production method used. The term is also used to denote the winding direction of fibers and strands of a rope.
Surface roughness, commonly referred to as simply roughness, is a measure of the total spaced surface irregularities. In engineering, this is what is usually meant by “surface finish.” A Lower number constitutes less of these irregularities on the surface. See chart below for roughness specifications/
Waviness is the measure of surface irregularities with a spacing greater than that of surface roughness. These irregularities usually occur due to warping, vibrations, or deflection during machining.
Many factors contribute to the surface finish in manufacturing. In machining, the interaction of the cutting edges and the micro-structure of the material being cut both contribute to the final surface finish.
In general, the cost of manufacturing a surface increases as the surface finish improves. Any given manufacturing process is usually optimized enough to ensure that the resulting texture is usable for the part’s intended application. If necessary, an additional process will be added to modify the initial texture. The expense of this additional process must be justified by adding value in some way—principally better function or longer lifespan. Parts that have sliding contact with others may work better or last longer if the roughness is lower. Aesthetic improvement may add value if it improves the sale-ability of the product.
Just as different manufacturing processes produce parts at various tolerances, they are also capable of different roughness’s. Generally, these two characteristics are linked: manufacturing processes that are dimensionally precise create surfaces with low roughness. In other words, if a process can manufacture parts to a narrow dimensional tolerance, the parts will not be very rough.
If you have any questions about your next project, one of our design engineers is ready to assist you.
Surface Roughness
Below is a comprehensive table to the different levels of surface roughness and their regional conversions.
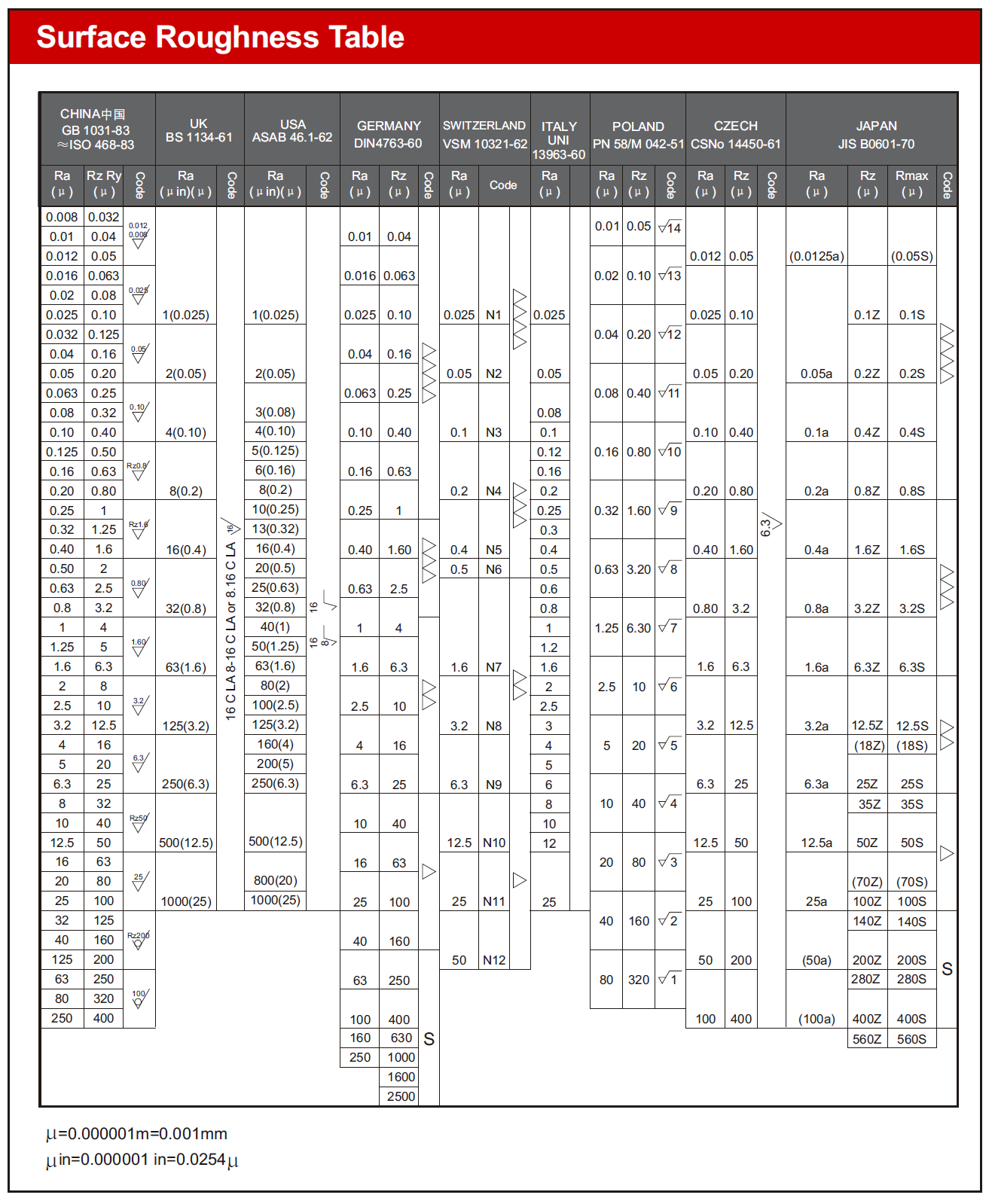
Recent Comments