Design Engineer Tip: Adding Radii
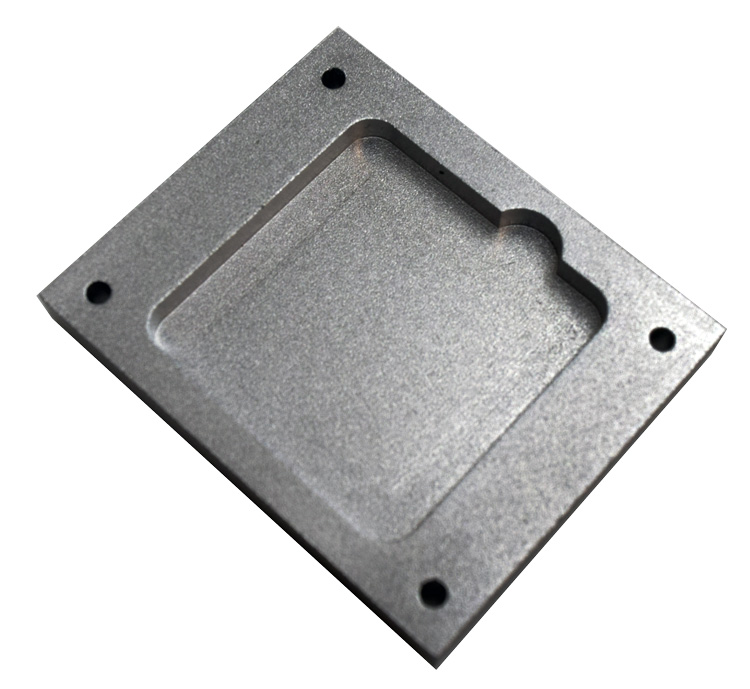
Does your part need to be machined to inscribe a shape within it? This process is called Profile Milling. For our example, we are looking at milling a square shape, with depth, within a cube see fig. 1 and fig. 2 examples below.
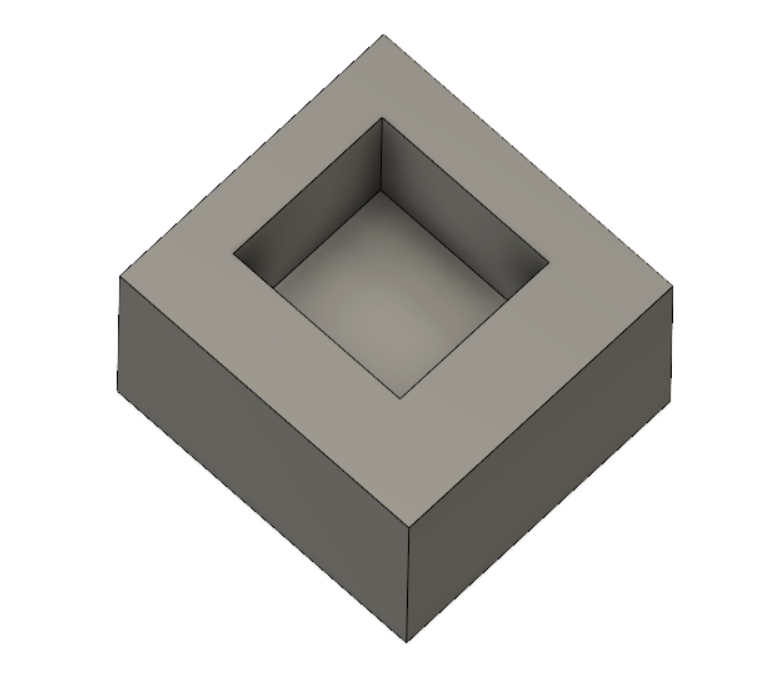
Fig. 1: Rendering: Inscribed part with square corners.
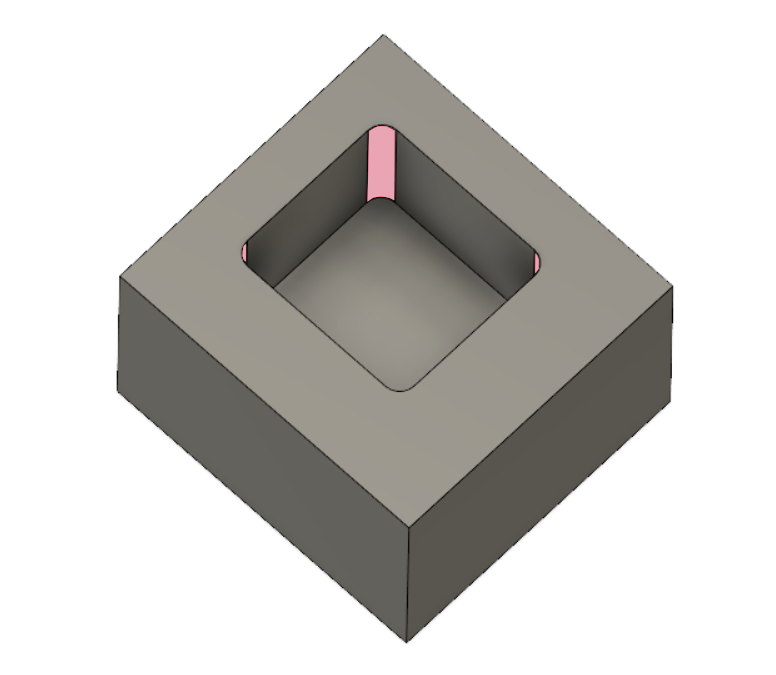
Fig. 2: Rendering: Inscribed part with radii added.
In standard machining practice, radii are needed for inside corners because sharp corners cannot be machined by an end mill. The CNC machine tool has only one direction to enter the cutting space, from the top. Additionally, the tool cannot pass all the way through the part, so the rotation of the tool naturally leaves rounded inseams and corners.
There are methods to creating square interior corners for profile milling. One way of machining sharp corners is with Electrical Discharge Machining (EDM). EDM is a machining process that creates a desired shape by using a series of rapidly recurring electrical current discharges. PartsBadger design engineer Nick Krumbiegel says, “Although EDM is the preferred method for achieving square interior corners, it is an expensive process. If your part can include radii and still fit into the scope of your final engineered design, this will create a cost efficiency to machining the part”. If your part needs square cornering, ask one of our design engineers about all the options available to achieve it.
It is important to add radii to your design if you are looking to utilize standard machining end mill practices. This saves time in the pre-production process, and cost for the part. If you need assistance in setting up your design file or choosing the radii size, please ask one of our design engineers. They stand by ready to help you make your next machined part.
Recent Comments