Steels, Stainless Steels, Tool Steels & Alloys
Steels: Defining the types, grades and classifying series.
Steel is an alloy that contains an iron base which is combined with carbon and other elements. In theory, all steels are iron alloys but for classification purposes there are four groups that common steels fall into: Carbon Steels, Alloy Steels, Stainless Steels and Tool Steels.
Carbon Steels
Carbon steels are primarily alloyed with carbon and account for roughly 90% of all steel production in the world. To be classified as a carbon steel, it must abide by the following:
- Contains no noted chromium, cobalt, molybdenum, nickel, niobium, titanium, tungsten, vanadium or zirconium.
- Contains no more than 0.60% copper
- Contains no more than 1.65% manganese
- Contains no more than 0.60% silicon
Earth is made up of roughly 35% Iron by mass. The majority of which is in Earths solid core.
- Low Carbon Steels/Mild Steels contain up to 0.3% carbon
- Medium Carbon Steels contain 0.3-0.6% carbon
- High Carbon Steels contain more than 0.6% carbon
No carbon steel can contain more than 2.1% carbon by weight. Sometimes carbon steels can be categorized as alloy steels, but technically they should fall into two separate groups.
Carbon & Alloy Steel SAE Series:
1000 Series– Carbon steels
2000 Series– Nickel steels
3000 Series– Nickel-chromium steels
4000 Series– Molybdenum steels
5000 Series– Chromium steels
6000 Series– Chromium-vanadium steels
7000 Series– Tungsten steels
8000 Series– Nickel-chromium-molybdenum steels
9000 Series– Silicon-manganese steels
Stainless Steels
Stainless Steels (sometimes known as inox steels) are known for their corrosion resistance and contain a minimum of 10.5% chromium and a maximum of 1.2% carbon by mass. The higher the chromium content, the higher the corrosion resistance. Many other elements can be added to increase or decrease certain properties, but all stainless steel grads fall into one of four main categories.
- Contain high levels of chromium and nickel
- Typically non-magnetic (can become slightly magnetic after cold working)
- Excellent corrosion resistance
- High ductility / formability
- Weldable
- Cannot be heat treated, but cold working can add significant strength
- Classified in the 200 & 300 series of stainless steels
- Contain high levels of chromium (no nickel)
- Strongly magnetic
- Good corrosion resistance (can be improved by increasing chromium and molybdenum)
- Good ductility, toughness and weldability (can be improved by decreasing carbon and nitrogen)
- Cannot be heat treated, but cold working can add significant strength
- Classified in the 400 series of stainless steels
- Due to containing less chromium and nickel than austenitic steels, ferritic steels are typically less expensive
- Contain high levels of chromium and smaller levels of carbon
- Typically are strongly magnetic (certain hardened martensitic steels lose their magnetism)
- Fair corrosion resistance, not as good as ferritic or austenitic steels
- Can be hardened to extreme strengths, although this can reduce toughness and makes it brittle
- In some grades, the carbon is replaced with nickel to increase toughness and corrosion resistance
- Commonly used in engineering and wear-resistant applications. Pocket knives are made out of martensitic steels
- Classified in the 400 series of stainless steels
- Contain roughly a 50/50 mix of austenite and ferrite
- Typically magnetic
- Excellent corrosion resistance
- Excellent strength and fabrication properties
- Machining can be more difficult due to strength, but is still possible
Stainless Steel SAE Series:
Type 102– Austenitic general purpose stainless steel
200 Series– Austenitic chromium-nickel-manganese alloys
300 Series– Austenitic chromium-nickel alloys
400 Series– Ferritic and martensitic chromium alloys
500 Series– Heat-resisting chromium alloys
Alloy Steels:
Technically, stainless steels and tool steels can be considered alloy steels. But for the sake of grouping them separately, alloy steels are steels that meet one of the following conditions:
- Contains more than 1.65% maganese, 0.60% silicon, or 0.60% copper
- Contains any specified amount of any other element to obtain an alloying effect. If the alloy steel contains chromium, it must be less than 3.99%
In general, alloying elements are added in lower percentages (less than 5%) to increase strength. When elements make up over 5% of the alloy it is usually to obtain special properties such as corrosion resistance, temperature stability or machinability.
How certain elements affect alloy steels:
Bismuth– Improves machinability
Boron– Significantly improves hardenability
Chromium– Increases hardenability and corrosion resistance
Copper– Improves corrosion resistance
Lead– Improves machinability
Manganese– Reduces brittleness and increases hardenability
Nickel– Increases corrosion resistance and toughens
Silicon– Increases strength and improves magnetic properties
Tungsten– Increases melting point
Tool Steel
Tool steel refers to certain carbon and alloy steels that have significant hardness and resistance to high temperatures, abrasion and deformation. They are commonly used in the shaping of other materials.
Depending on what properties are required, there are six groups of tool steels. Water hardening, air hardening, high carbon chromium, shock resisting, oil hardening and hot working. Hot working steels (H series) are the only ones designed for use at high temperatures and all other groups are typically used at room temperature but can be appropriate for applications up to 300°F.
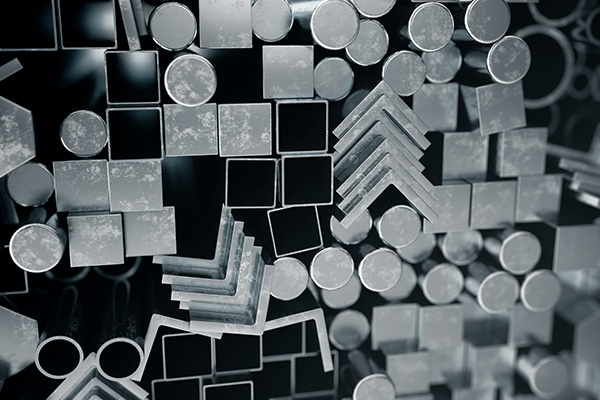
Water Hardening (W Series)
Water hardening steels are hardened by water quenching and are the most common tool steel due to their low cost. They can maintain significant hardness but tend to be more brittle when compared to other tool steels. Around 300°F these steels begin to soften and are generally not suited for high temperature applications.
Air Hardening (A Series)
Air hardening steels are known to be all purpose tool steels that contain a high amount of chromium to reduce distortion during the heat treatment process. They have great machinability, wear resistance and toughness and are known to be a good balance between D series and A series tool steels.
High Carbon-Chromium (D Series)
Containing high amounts of carbon and chromium (10-13%), the D series tool steels retain their hardness up to roughly 800°F and are commonly used in forges and die-casting applications. Having a high chromium content they can sometimes be classified as stainless, however D series tool steels have a very limited corrosion resistance.
Shock Resisting (S Series)
Shock resisting steels can resist high volumes of shock at both high and low temperatures, where other tool steels may tend to crack in these conditions. They contain a low amount of carbon (0.5%) and varying amounts of molybdenum, tungsten, chromium, silicon and manganese. A common use of S series steels is in jackhammer bits.
Hot Working (H Series)
Hot working steels are designed to cut or shape other materials at high temperatures. They maintain high levels of strength and hardness during long exposure to elevated temperatures. They contain a low amount of carbon and a moderate amount of other alloying elements.
Oil Hardening (O Series)
O Series steels are hardened in oil at around 1450°F and then tempered at cooler temperatures (less than 400°F). They are typically used in woodworking tools, cutting tools and knives and can be hardened up to 66 HRC.
PartsBadger offers machining of many types of steel.
Rapid Quote
Enter your material, finish, tolerance, quantity, and upload your file to get your own custom quote in 2-6 hours. The Rapid Quote is perfect for higher volumes or special features.
Instant Quote
Enter your dimensions, material, finish and any other features your part needs and let our Instant Quote algorithm give you immediate pricing.
Contact Us
Need reverse engineering, design services, or just want to work with a design engineer one-on-one? Contact Us Now!