Aluminum Alloys: Defining the different series and their machinability.
Aluminum alloys offer a wide range of properties such as flexible, weldable, high strength, corrosion resistance and light weight. Due to it’s low cost and formability, aluminum is often the first choice for prototyping and can be used in nearly any industry for a variety of applications.
When it comes to machining we need to focus on wrought alloys as opposed to cast alloys. Wrought alloys are mechanically altered (rolled, forged, extruded, drawn) and maintain their properties quite well. Cast alloys are formed from liquid molten metal and often contain a high percentage of silicon. During the casting process the alloy can lose a significant amount of its mechanical properties and this makes it less ideal for machining.
Aluminum
Aluminum (AI) is a soft silvery-white and nonmagnetic element that is known to be the top metal choice for many industrial uses. Its properties include high strength, low density and can be resistance to corrosion through a process called Passivation.
Aluminum Alloys
In order to enhance or add certain properties, Aluminum is commonly combined with other elements to form Aluminum alloys. Within these alloys, Aluminum is the predominant Material. To be considered an Aluminum alloy, the additional elements added must not exceed a total of 15% of the overall composition.
Depending on which elements are added to the aluminum, the resulting alloy can have many different strengths and weaknesses. When considering which alloy to use for machining processes we need to understand how the added elements affect the alloys machinability. Machinability is a loose term but general stands for the ease of which the alloy can be machined.
Earth is made up of 1.59% Aluminum by mass. The majority of which is in the Earth’s crust.
How certain elements affect the machinability of aluminum alloys:
Factors to consider when machining Aluminum:
Equipment
The cutting tool selection is crucial when machining aluminum. Pure aluminum is soft by nature and can form a gummy buildup when being cut or machined. In extreme cases the material can can actually fuse to the cutting edge in what is called Edge Adherence. A high speed cutting tool coated with either Diamond or DLC coating are universally known to be highly effective in machining aluminum.
Composition of the Alloy
The alloying elements need to be considered when determining machinability of an Aluminum alloy. Higher contents of Bismuth, Magnesium, Lead
Defining the different series of Aluminum Alloys:
1000 Series– Contain a minimum of 99% Aluminum and can be work hardened to increase strength. Often used in chemical containment, food packaging and electrical applications.
2000 Series– Alloyed primarily with Copper and can be hardened to strengths similar to steel. Often used in aerospace applications.
3000 Series– Alloyed primarily with Manganese and can be hardened and heat treated. Often used in beverage cans, cookware and industrial high heat applications.
4000 Series- Alloyed primarily with Silicon. Often used in applications where a lower melting point in the alloy is needed, such as casting and welding. If Magnesium is added to a 4000 series alloy it can be heat treated and transformed into a 6000 series alloy.
5000 Series– Alloyed primarily with Magnesium and offers high corrosion resistance. Often used in marine applications. 5083 alloy is common and has the highest strength of non heat treated alloys.
6000 Series- Alloyed primarily with a combination of Magnesium and Silicon and can be one of the most versatile of the Aluminum Alloys. It is considered an all-purpose aluminum due to its high machinability and strength. 6061 alloy is the most common of all Aluminum alloys and is used in many applications.
7000 Series– Alloyed primarily with Zinc and can be hardened to the highest strength of any Aluminum alloy. Often used in aerospace applications.
Common Industry Uses
Aerospace / Aircraft
With properties including high strength, light weight and efficient heat transfer, the following alloys are common in aerospace and aircraft applications.
- 1420
- 2004, 2014, 2017, 2020, 2024, 2080, 2090, 2091, 2095, 2219, 2324, 2519, 2524
- 4047
- 6013, 6061, 6063, 6113, 6951
- 7010, 7049, 7050, 7055, 7068, 7075, 7079, 7093, 7150, 7178, 7475
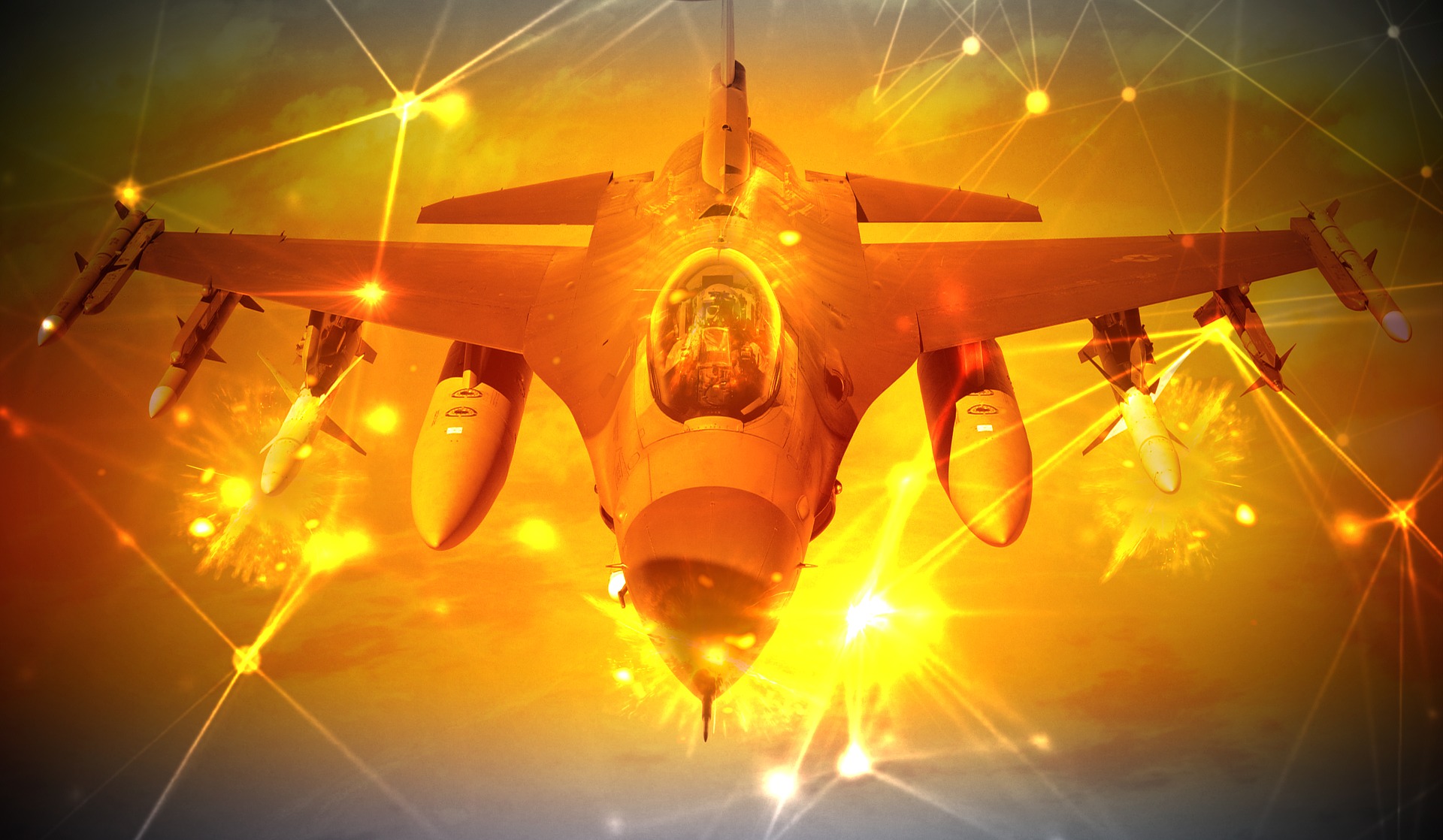
Marine / Offshore
Non heat treated alloys (5000 series) are preferred in marine applications due to their high corrosion resistance. Magnesium adds both strength and corrosion resistance as well as increasing the ability to be welded.
In high humidity, underwater and salt water environments, the following alloys are popular:
- 5052, 5059, 5083, 5086
- 6061, 6063
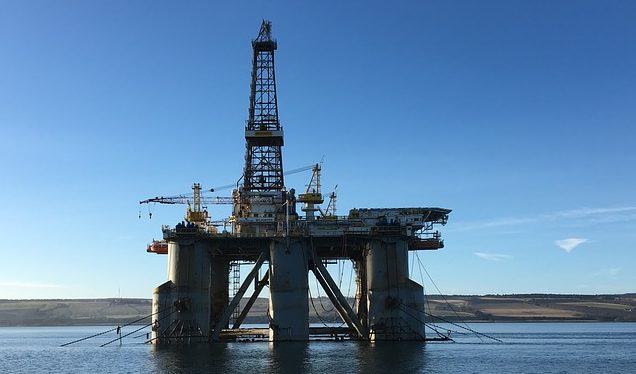
Automotive / Cycling
Due to their light weight and strength, the following allows are preferred for cycling frames and parts.
- 2014
- 6061, 6063
- 7005, 7075
For automotive manufacturing, aluminum alloys are the first choice for external body parts and other components.
- 2008, 2036, 5083, 5456, 5754, 6016, 6111 are common alloys for body panels.
- 5182, 5754, 6061, 6063 are common alloys for automobile frames
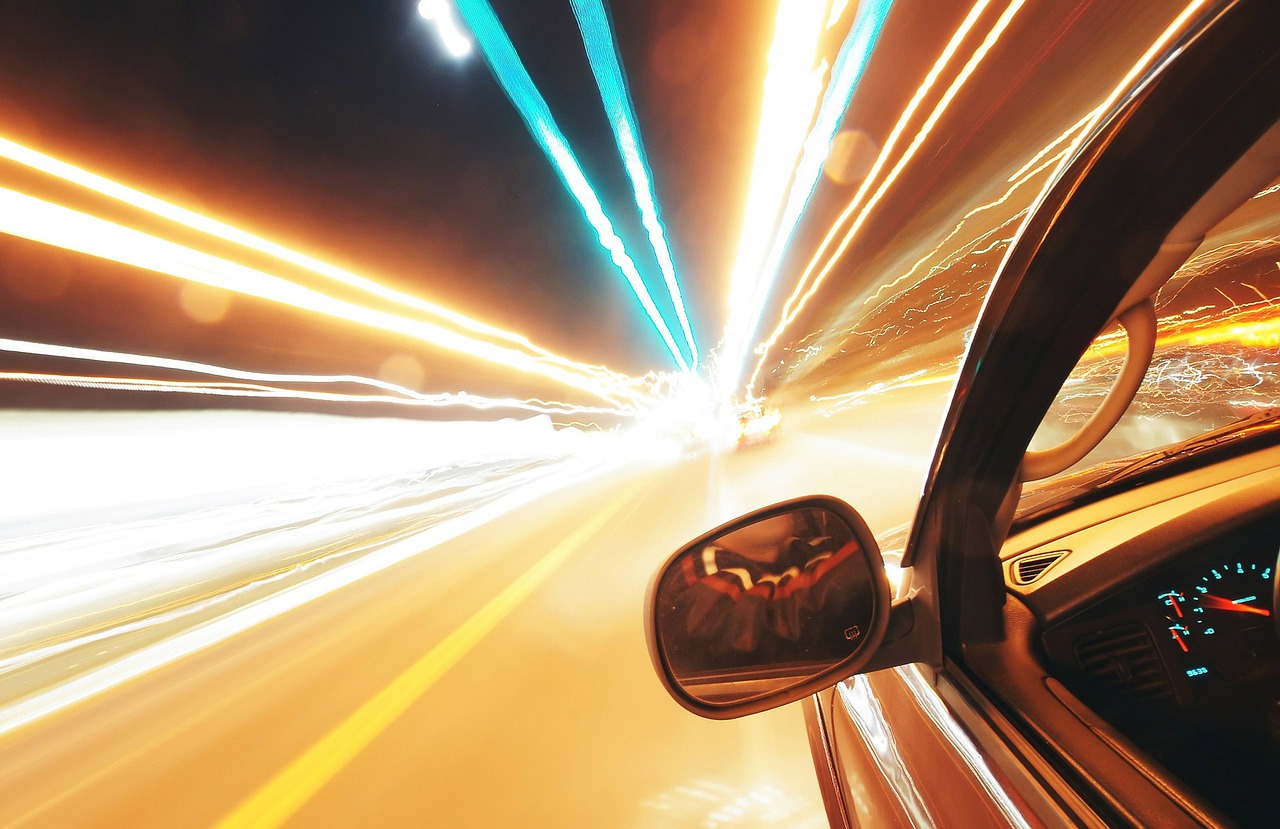
PartsBadger offers machining of nearly every type of Aluminum Alloy.
Rapid Quote
Enter your material, finish, tolerance, quantity, and upload your file to get your own custom quote in 2-6 hours. The Rapid Quote is perfect for higher volumes or special features.
Instant Quote
Enter your dimensions, material, finish and any other features your part needs and let our Instant Quote algorithm give you immediate pricing.
Contact Us
Need reverse engineering, design services, or just want to work with a design engineer one-on-one? Contact Us Now!