Sheet Metal Bending
Sheet metal bending is a deformation process that involves using a machine called a brake to bend metal. Metal can be bent into U shapes, V shapes, or channel to an angle of up to 120 degrees. It’s an efficient form of deformation that allows the metal to be formed into a new part. Unlike laser cutting, this is the simplest form of sheet metal forming.
Press brakes use a die and punch to bend a piece of metal. The metal lies on the die, the solid block, in position where it will be bent in a certain way. From there, a punch force will come down on the metal and bend it into that new shape, forming a new part. The simplicity of this can take seconds per part, which makes this very efficient. Compared to the complexity of laser cutters, there is no coding needed for this.
Even though it is simple, there are certain things to know. In fact, there are multiple press brakes that are beneficial for certain jobs.
Types of Press Brakes
Hydraulic Press Brakes
Hydraulic press brakes are the oldest and most common press brake. They are used for both specialized sheet metal work and continuous production. The hydraulic press brake uses a cold working process. The cold working process forms cold formed steel. This process is done in room temperature and is used for rolling, pressing, stamping, bending, and other similar press forms.
These press brakes apply pressure via hydraulics with more control on the user’s end. This gives a more precise, accurate, and customizable bend to each product. The control and precision gives this press brake its popularity. The only downside is the need for hydraulic oil to run the press. This also means that hydraulic oil depends on the temperature too. Temperature changing too much could leave the oil unstable. Too high of temperature would affect the speed and bending accuracy of the press.
Electronic Press
Electronic press brakes are the newest and least common press brakes. Unlike hydraulic press brakes, electronic presses don’t need any oil to run. Electronic motors only run when necessary, so operating costs are lower with less energy used. This type of press brake has more features. With the more features, there is more accuracy, precision, and customization, and speed.
These presses use less CO2 and cost less for maintenance. Other benefits include:
- Adjustable bending speed
- Faster slider speed
- Benefits the environment
- Energy saving
With it being newer technology, electronic presses errors can be hard to predict how to fix. Another issue with electronic press brakes are the fact that they are so compact. Since they are smaller, they can only be used for smaller parts with a limited amount of tons. Both of these presses can bend metal in a variety of different ways.
What is deformation?
First, it’s important to understand what deformation is. According to Corrosionpedia, deformation is the modification of the shape or size of the metal object due to an applied force or change in temperature. Deformation is mainly caused by pulling, twisting, pushing, shearing, and bending. Techniques of deformation range from laser cutting to sheet metal bending. Deformation is the umbrella term for all changes in metal objects, including metal bending.
Sheet Metal Bending Techniques
V-Bending
V-Bending is the most common form of bending. This type of bending creates many different parts. The part lies on a V-shaped indented die. Once ready, a V-shaped punch pushes down on the metal. This punch bends the metal into a V-shape, as well. The bends’s angle depends on the pressure point of the punch. From there, it can go through 3 processes.
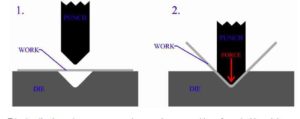
This diagram shows the sheet metal bending process of v-bending.
V-Bending Sheet Metal Bending Processes
Bottoming
Bottoming is a version of V-Bending that bends the metal’s focal point all the way down to the bottom of the V-die. The shape of the V-shaped part depends on the pre-set size of the V-shaped die. This creates more accuracy and permanence in the bend. There will not be a spring-back. A spring-back occurs when a metal goes back to its former shape after being partially bent.
Coining
Coining is a version of V-Bending that is very similarly to bottoming. The V-shaped punch forces the metal to the bottom of the V-shaped die. The only difference is that the punch is much smaller and distinguishable. Coining with a press brake involves using enough tonnage to conform the sheet metal to the exact angle of the punch and die.
Air Bending
Unlike the previous two V-Bending methods, air bending is less accurate. Air bending is a partial bend of the metal part. The technique is simple by not needing tools. In air bending, a bend angle is formed by driving the punch into the sheet metal to a specific position within the die opening. This type of method is capable of having spring-back though.
The dangers of spring-back are the shape and size of the parts do not fit the working surface anymore. This affects the assembly precision of the products.
Other Sheet Metal Bending Techniques
U-Bending
U-Bending is very similar to V-Bending. It has a very similar process of laying on a U-Shaped die. The punch forces the part to the bottom of the die. This can create bottoming, coining, or air bending. The only difference is that U-Bending is less common.
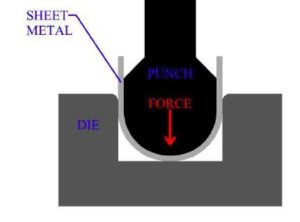
This diagram shows the process of U-Bending.
Step Bending
Step bending is the process of continuous V-bending to get a product with a large radius. This makes it possible to create large products with normal tools for a cheaper price. This is one of the most creative metal bending techniques. The disadvantage of this is that it needs to be bent perfectly to avoid misalignment.
Roll Bending
Roll bending is used for making tubes or cones in different shapes. Large radius bends use this technique. Depending on the machine’s capacity and number of rolls, one or more bends can be done simultaneously.
In the process, there are two driving rolls and a third adjustable one. This one moves along via frictional forces. If the part needs to be bent at both ends as well as the mid-section, an extra operation is required. This is done on a hydraulic press or press brake. Otherwise, the edges of the detail will end up flat.
Wipe Bending
Wipe bending, or edge bending, is another way to bend sheet metal edges. It is important to make sure that the sheet is properly pushed onto the wipe die. As a result, the wipe die also determines the bend’s inner radius. The slack between the wipe die and the punch plays an important role in getting a good result.
Using wipe bending has the advantage of being repetitive and needing less skill to perform. Wipe bending’s disadvantage is that spring-back can often occur. To control spring-back, the top of the bend is often coined by adding a return flange to the forming punch and putting the tooling under such pressure that it begins to flow. This can weaken the metal and quality of the part.
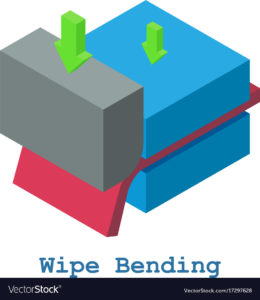
This diagram shows the process of wipe bending.
Rotary Bending
Another way to bend edges is through rotary bending. It has a big advantage over wipe bending or V-bending – it does not scratch the material’s surface. There are special polymer tools available to avoid any kind of tool marking, let alone scratches. Rotary benders can also bend sharper corners than 90 degrees. This helps greatly with such common angles, as spring-back is not a problem any more. Another advantage of using rotary bending is the simplicity of adjusting the angle. It doesn’t take long to grind the height of the assembly.
A disadvantage of this technique is that it is expensive. Although the cost-saving in the long run of this machine can outweigh the initial cost. The most common method is with 2 rolls but there are also options with one roll. This method is also suitable for producing U-channels with flanges that are close by, as it is more flexible than other methods.
We Are Your Online CNC Machine Shop
Parts Badger creates your exact designed product. We use Instant quoting and 24/7 manufacturing to get your products created and back to you very quickly. Our services include but are not limited to:
Our knowledgeable team of experts will work closely with you to create high-quality components fabricated to your unique specifications, regardless of complexity. Contact us or request your rapid quote today to work with us on your next project.
Recent Comments